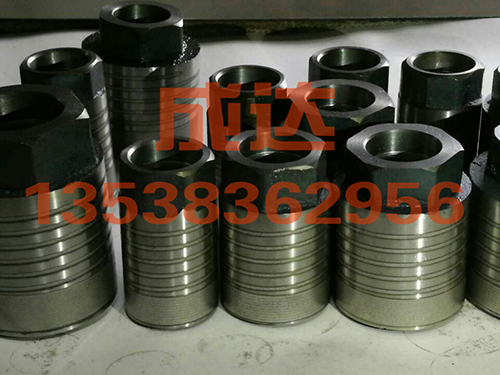
Ceramic plunger head adopts new technology and nano-ceramic treatment technology to make high-performance wear-resistant layer on the surface of the plunger head, improve the friction and lubrication mechanism, enhance the wear resistance, and greatly improve the plunger head’s performance. Service life.
Performance advantages of ceramic plunger head:1. Excellent wear resistance. A 0.5CM-thick ceramic wear-resistant layer is prepared on the surface of the plunger head using nano-ceramic technology, and the surface hardness is about HV450-800.
2. The performance of the ceramic layer is stable, and the metallurgical combination with the plunger head substrate is achieved, and there will never be peeling during use
3. The surface of the plunger head is treated with ring-shaped ceramics, which is conducive to storing lubricant, improving the lubrication performance, and reducing the wear on the barrel.
4. The use performance is more stable. Compared with the ordinary ductile iron plunger head, the life of the 160T-1250T die casting machine can be increased by 20-25 times, and the average life span is 15000-20000 mold times. Under good industrial and mining conditions , It can reach 30,000 mold times, and the same period of use can reach 5-7 days
Improve production capacity and save energy:The replacement time of ordinary punches takes 20-30 minutes per shift, while it takes 15-20 minutes for ceramic laser punches about 5-7 days. A ceramic laser punch can save about 2 times compared with a normal punch replacement time. Hours, not only increased the production capacity of 2 hours, but also saved 2 hours of energy, greatly improving the production efficiency.
Reduce the scrap rate:The replacement of the ordinary punch with a new punch will produce 2 wastes each time, while the ceramic laser punch is replaced every 5-7 days, thus reducing 10 wastes.
For example: Calculating at 10 yuan per waste, 5-7 days will save more than 100 yuan, which can save more than 20,000 yuan a year.
Instructions for use:1. Ensure that there is good concentricity between the punch, the material tube and the sprue bushing, and a good fit is poor to avoid strains, scratches and unilateral wear.
2. Ensure that the punch has normal and good cooling and lubrication to avoid strain or cracking on the thermal fatigue surface.
3. The inner hole between the material tube and the sprue sleeve must not be misaligned, otherwise the punch will wear out and peel off on one side.
4. After the punch is installed, it is necessary to melt the aluminum alloy 7-10 times to make the punch, the material tube and the sprue sleeve have the same temperature.
Dongguan Chengda Machinery Parts Co., Ltd. (Wangda Die-casting Machine Parts Factory) is located in Dongguan City, an industrially developed Pearl River Delta region. For many years, our company has integrated R&D, production, sales, internal and external circular grinding, vacuum heat treatment, Vacuum nitriding and maintenance are integrated modern technology enterprises. Our company has a group of technical teams and sales teams with more than 10 years of experience in die casting machine parts processing, as well as high-precision production equipment, including CNC lathes, automatic lathes, milling machines, grinding machines (internal and external cylindrical grinding), and vertical grinding , Wire cutting, boring machine, gantry milling machine, vacuum heat treatment furnace, vacuum nitriding furnace, quenching furnace, etc. The production capacity is greatly improved, and various production tasks proposed by customers can be completed efficiently and quickly. The product quality is more guaranteed and the delivery time is more punctual.
Processing, production and sales: Die-casting machine parts, Lijin, Yizumi, Fulai, Buhler, Hishinuma, Kazuka, Xingxing, Chenfeng, Weitai, Yousheng, Xinhong, Mingcheng, Zhengao, Noda, Ube , Toshiba, Toyo, Baoyang, etc. 15T-650T hot chamber zinc and magnesium alloy die-casting machine: material pot, nozzle body, nozzle head, piston ring, hammer head, heating sleeve, heating cake, temperature control rod and other accessories; 125T-4500T cold chamber aluminum, magnesium alloy : Barrel, plunger head, injection rod, connector, plunger oil, crucible, release agent, spray gun, pellet oil, melting furnace, pellet machine, manipulator, mold accessories: firing pin, firing pin sleeve, etc.; die-casting Machine maintenance, material pot replacement, etc.; the company has a complete and scientific quality management system. Integrity, strength and product quality have been recognized by the industry. Friends from all walks of life are welcome to visit, guide and negotiate business.
Relying on its professional level and mature technology in the field of die-casting machine parts, as well as its diversified information advantages in the Pearl River Delta, Chengda has adopted foreign advanced processing, heat treatment, and nitriding technologies through years of technical practice, research and development and innovation. , The service life of parts is equal to the service life of imported parts. The die-casting machine parts produced by our company are sold all over the country and exported to Singapore, Vietnam, Taiwan and other regions.