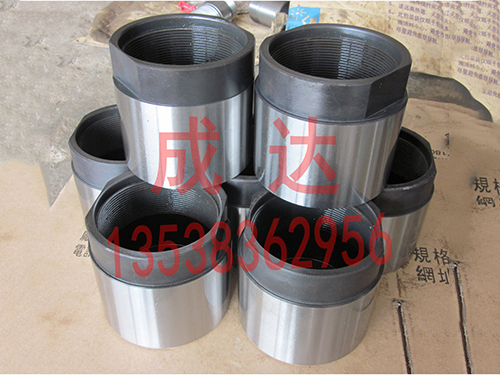
The alloy wear-resistant punch is made of special hot work die steel. The surface is strengthened by HRC38~46, which can protect the melting cup very well (lower hardness will not damage the melting cup). The life of the punches under normal use is about 15,000-25,000 die times. The average service life of ordinary ductile iron punches is one shift (8 hours), while the average service life of alloy wear-resistant punches is about 5-7 days. The service life of alloy wear-resistant punches is more than 15 times that of ordinary ductile iron punches.
The replacement time of ordinary ductile iron punches takes 15 minutes per shift, while the replacement time of alloy wear-resistant punches only takes 15 minutes per week. The alloy wear-resistant punch saves 5 hours of replacement time per week, increases the output of 5 hours, saves 5 hours of energy, and significantly improves production efficiency.
Instructions for use:1. Ensure that the punch, the pressure chamber, and the sprue sleeve have good concentricity and good tolerances to avoid strain, scratches or unilateral wear on the surface of the punch.
2. Ensure that the punch has good cooling and good lubrication to avoid cracking or surface strain due to thermal fatigue.
3. The inner hole of the melting cup and the mold sprue sleeve must not be misaligned, otherwise the punch will be worn out on one side, and the end face of the nickel and cobalt punch will peel off and be strained due to shear.
4. After the punch is installed, it needs to be preheated 5~10 times with molten aluminum alloy, so that the punch, melting cup and sprue sleeve are preheated to about 200oC at the same time, and the punch expands under force to ensure that the punch and The fit gap of the melting cup is idealized.
Diameter (mm) |
Ø40 |
Ø50 |
Ø60 |
Ø70 |
Ø80 |
Ø90 |
Ø100 |
Ø110 |
Ø120 |
Ø130 |
Ø140 |
Length (mm) |
80 |
90 |
90 |
90 |
100 |
120 |
140 |
120 |
140 |
140 |
140 |
Thread |
M27X2 |
M30X2 |
M30X2 |
M30X2 |
M42X2 |
M42X3 |
M60X4 |
M60X4 |
M60X4 |
M72X2 |
M72X2 |
Dongguan Chengda Machinery Parts Co., Ltd. (Wangda Die-casting Machine Parts Factory) is located in Dongguan City, an industrially developed Pearl River Delta region. For many years, our company has integrated R&D, production, sales, internal and external circular grinding, vacuum heat treatment, Vacuum nitriding and maintenance are integrated modern technology enterprises. Our company has a group of technical teams and sales teams with more than 10 years of experience in die casting machine parts processing, as well as high-precision production equipment, including CNC lathes, automatic lathes, milling machines, grinding machines (internal and external cylindrical grinding), and vertical grinding , Wire cutting, boring machine, gantry milling machine, vacuum heat treatment furnace, vacuum nitriding furnace, quenching furnace, etc. The production capacity is greatly improved, and various production tasks proposed by customers can be completed efficiently and quickly. The product quality is more guaranteed and the delivery time is more punctual.
Processing, production and sales: Die-casting machine parts, Lijin, Yizumi, Fulai, Buhler, Hishinuma, Kazuka, Xingxing, Chenfeng, Weitai, Yousheng, Xinhong, Mingcheng, Zhengao, Noda, Ube , Toshiba, Toyo, Baoyang, etc. 15T-650T hot chamber zinc and magnesium alloy die-casting machine: material pot, nozzle body, nozzle head, piston ring, hammer head, heating sleeve, heating cake, temperature control rod and other accessories; 125T-4500T cold chamber aluminum, magnesium alloy : Barrel, plunger head, injection rod, connector, plunger oil, crucible, release agent, spray gun, pellet oil, melting furnace, pellet machine, manipulator, mold accessories: firing pin, firing pin sleeve, etc.; die-casting Machine maintenance, material pot replacement, etc.; the company has a complete and scientific quality management system. Integrity, strength and product quality have been recognized by the industry. Friends from all walks of life are welcome to visit, guide and negotiate business.
Relying on its professional level and mature technology in the field of die-casting machine parts, as well as its diversified information advantages in the Pearl River Delta, Chengda has adopted foreign advanced processing, heat treatment, and nitriding technologies through years of technical practice, research and development and innovation. , The service life of parts is equal to the service life of imported parts. The die-casting machine parts produced by our company are sold all over the country and exported to Singapore, Vietnam, Taiwan and other regions.