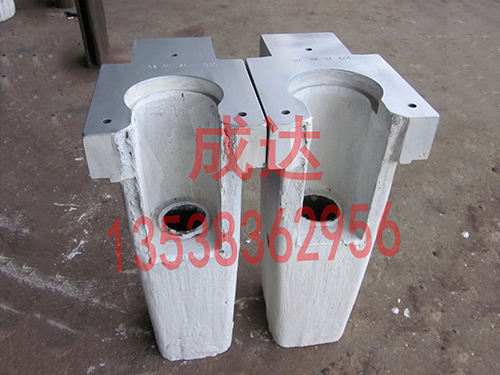
The pot assembly has been installed during the machine assembly. When the machine is sent to the customer, the pot assembly should be removed and reinstalled on the machine after the furnace is installed. The pot assembly is installed on the stand of the machine. The function is to inject and transport the alloy liquid. The installation method and steps of the pot assembly are as follows:
1. Place the pot on the top of the stand arch, and the side of the potty pot protrudes 1~3mm from the assembly surface of the stand side.
2, first assemble the two pressure plates on the upper surface of the pot, tighten them properly with a wrench, and then assemble the side pressure plates.
3. Tighten the 4 screws on the side pressure plate evenly and alternately with an Allen key;
4. Use a wrench to further tighten the two pressure plate screws on the upper surface.
Requirements: All pressure plate screws should be coated with a thin layer of high temperature grease on the external threads before installation. Our company currently uses "OPES High Temperature Grease" produced by OPEX Petroleum Company.
Requirements for use:1. The gooseneck of the material pot is heated by heating rods or heating cakes. When the machine is working normally, the heating temperature is controlled at 420 ℃: ①, use heating rods to heat, and control the temperature at 420 ℃; ②, use heating cakes, start working Make sure that the gooseneck is unblocked. Prevent the zinc alloy material from being blocked in the gooseneck, and the material cannot be injected normally;
2. The composition of the die-cast zinc alloy must meet the requirements of GB/T13818-92, and the impurity content has a great influence on the corrosion resistance of the pot.
Maintenance Rules1. Before the pot is used, NC8 anti-acid coating must be applied to the surface of the pot casting to prevent corrosion of the pot casting; (painted before leaving the factory)
2. Control the temperature of the zinc alloy material in the crucible at 410~430℃. Preventing excessively high temperature will sharply increase the corrosion of the zinc alloy liquid, causing corrosion of the pot body and barrel, blocking the injection punch, and reducing the service life of the pot. (When the material temperature is normal, the zinc alloy liquid is grayish white; when the material temperature is too high, it is dark red)
3. Check the furnace probe once every half a month, pull out the furnace probe, and wipe the surface clean. Check whether it is directly corroded, and replace it if corrosion is found;
4. Clean up the alloy slag on the liquid surface of the zinc alloy in the crucible in time. Once the alloy slag enters the pot holder, it will strain the steel wire, the injection punch, and the pot holder, and the injection punch will be blocked in severe cases. ;
5. Add alloy material in time, keep the zinc alloy liquid level not lower than the crucible one, and prevent the alloy liquid level from being too low. The alloy can easily enter the barrel and jam the injection stamping;
6. The zinc alloy material should be kept clean and free of moisture, oil and other impurities;
7. Use a nozzle with a taper that matches the gooseneck taper hole.
8. If material leakage is found in the gooseneck taper hole, the nozzle body should be disassembled immediately, and the taper surface alloy liquid of the nozzle body should be cleaned first, then the alloy liquid in the taper hole of the gooseneck material pot should be cleaned, and finally the nozzle body should be cleaned. Install the step nozzle body installed; (see the nozzle body instruction manual)
9. Work stop time (downtime for mold change, mold repair, etc.) The temperature of the gooseneck and nozzle body should be adjusted to below 380℃ to reduce the corrosion of the gooseneck and nozzle (pay attention to re-die-casting the workpiece) The temperature of the gooseneck and nozzle body should be raised to the required working temperature beforehand)
10. If there is no production if it stops. Before stopping the machine, the injection punch (hammer head) should be disassembled, and the alloy liquid should be scooped out 2/3. Note that the furnace temperature probe cannot leave the alloy liquid surface.
11. Regular replacement of the steel order (recommended once a month and a half) and injection head (recommended once every four months);
12. When loading and unloading the injection punch and steel order, no debris should fall into the barrel.
Dongguan Chengda Machinery Parts Co., Ltd. (Wangda Die-casting Machine Parts Factory) is located in Dongguan City, an industrially developed Pearl River Delta region. For many years, our company has integrated R&D, production, sales, internal and external circular grinding, vacuum heat treatment, Vacuum nitriding and maintenance are integrated modern technology enterprises. Our company has a group of technical teams and sales teams with more than 10 years of experience in die casting machine parts processing, as well as high-precision production equipment, including CNC lathes, automatic lathes, milling machines, grinding machines (internal and external cylindrical grinding), and vertical grinding , Wire cutting, boring machine, gantry milling machine, vacuum heat treatment furnace, vacuum nitriding furnace, quenching furnace, etc. The production capacity is greatly improved, and various production tasks proposed by customers can be completed efficiently and quickly. The product quality is more guaranteed and the delivery time is more punctual.
Processing, production and sales: Die-casting machine parts, Lijin, Yizumi, Fulai, Buhler, Hishinuma, Kazuka, Xingxing, Chenfeng, Weitai, Yousheng, Xinhong, Mingcheng, Zhengao, Noda, Ube , Toshiba, Toyo, Baoyang, etc. 15T-650T hot chamber zinc and magnesium alloy die-casting machine: material pot, nozzle body, nozzle head, piston ring, hammer head, heating sleeve, heating cake, temperature control rod and other accessories; 125T-4500T cold chamber aluminum, magnesium alloy : Barrel, plunger head, injection rod, connector, plunger oil, crucible, release agent, spray gun, pellet oil, melting furnace, pellet machine, manipulator, mold accessories: firing pin, firing pin sleeve, etc.; die-casting Machine maintenance, material pot replacement, etc.; the company has a complete and scientific quality management system. Integrity, strength and product quality have been recognized by the industry. Friends from all walks of life are welcome to visit, guide and negotiate business.
Relying on its professional level and mature technology in the field of die-casting machine parts, as well as its diversified information advantages in the Pearl River Delta, Chengda has adopted foreign advanced processing, heat treatment, and nitriding technologies through years of technical practice, research and development and innovation. , The service life of parts is equal to the service life of imported parts. The die-casting machine parts produced by our company are sold all over the country and exported to Singapore, Vietnam, Taiwan and other regions.